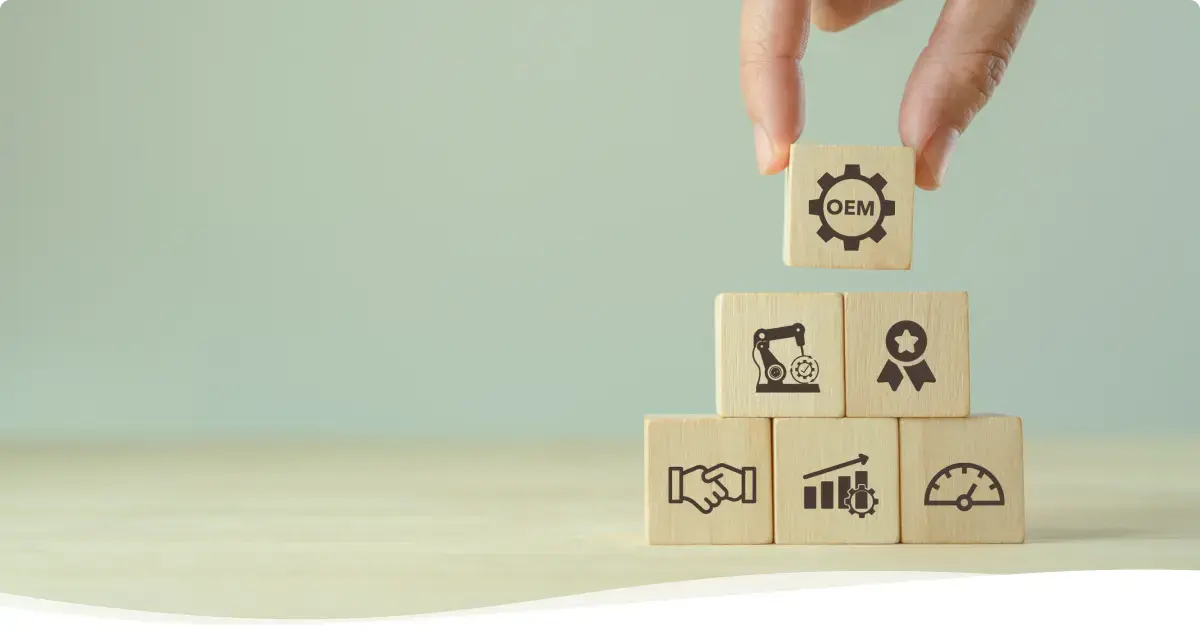
The Role of Vertically Integrated Manufacturing in OEM Success
OEM businesses continually grapple with uncertain supply chains, complex production processes and how to meet shifting market expectations despite the increasingly globalized manufacturing landscape, characterized by technological advancements. To make matters worse, the need to keep costs low and competitive advantage high has never been more pronounced.
Faced with improving manufacturing efficiency while ensuring business agility, OEMs need a more strategic solution to meet their mandate of maintaining market value. This is where vertically integrated manufacturing presents itself as a prudent approach to product manufacturing.
Understanding vertical integration
Vertically integrated manufacturing refers to the business strategy of a single manufacturing company owning and controlling most or all of the product supply chain. It involves integrating various stages of production, from the procurement of raw materials to the manufacturing of components and final assembly to the distribution of the finished product.
With vertically integrated manufacturing, the manufacturer can increase efficiency, cut costs, and enhance market competitiveness by controlling more aspects of the production and supply process. This also reduces dependency on multiple external suppliers, secures a more predictable supply of materials, and allows manufacturers to manage better the production process, product quality, and budgets.
Vertical integration first gained prominence in the late 19th and early 20th centuries, particularly in the steel and automotive manufacturing industries. Corporations like the Ford Motor Company could fully control resources and production processes, enhancing their competitiveness.
Ford's model of vertical integration involved owning every aspect of production, including rubber plantations for tires and mines for metal ore, as well as factories for assembly. This extensive control over the supply chain allowed Ford to drastically reduce the cost of production, thus lowering the price of the finished product and revolutionizing the automobile industry, directly contributing to the success of the global giant we're still familiar with today.
The significance of vertically integrated manufacturing for OEMs
Vertical integration holds significant strategic value for OEMs, especially when engaging with vertically integrated contract manufacturing partners. Partnering with a vertically integrated manufacturing company simplifies and enhances OEMs' supply chain and production processes, providing greater control across the entire value chain—from sourcing raw materials to final product assembly. This control is crucial for reducing dependencies on multiple suppliers, which often comes with problematic variability and uncertainty in the supply chain.
Cost savings and efficiency
In terms of cost savings and efficiency, vertical integration allows OEMs to streamline operations and reduce overhead costs associated with working with multiple contractors. By having a single supplier manage more of the production process, OEMs can implement changes cost-effectively, have greater control over product design, and coordinate manufacturing more efficiently, especially when working across multiple global regions. This integration supports faster adaptation to market changes or customer feedback, significantly shortening the time from product development to market.
Improved quality control
Moreover, vertical integration can enhance quality control across the production process. Contract manufacturers providing vertically integrated manufacturing services enforce stricter quality standards and ensure every part of the production process under their control adheres to these standards. This direct oversight can lead to higher-quality products, boosting customer satisfaction and brand reputation for OEMs further down the line.
Greater customer satisfaction
Vertically integrated manufacturing processes also offer OEMs greater customization options, further ensuring and maintaining product quality. With more control over more steps in the production process, contract manufacturers can offer their OEM customers tailored products that meet their specific requirements, allowing them to respond promptly to service requests or product issues. This capability not only differentiates the OEM in a competitive market but also builds stronger customer relationships, enhancing long-term business prospects.
Enhanced scalability
By owning or closely managing more steps in the supply chain, vertically integrated contract manufacturers can adjust production levels more rapidly and efficiently, as and when OEMs require. This direct oversight and single line of communication eliminates delays and complications typically seen when coordinating multiple external suppliers, dramatically enhancing OEM scalability. Additionally, as vertically integrated manufacturing partners have better control over production schedules, they can optimize resource usage, reduce waste and help OEMs manage expansion costs more effectively, facilitating rapid growth for scaling businesses.
Key elements of the vertically integrated manufacturing process
A well-tuned vertically integrated manufacturing process includes numerous steps along the product value chain, providing a more comprehensive production line from beginning to end.
Optimal vertical integration services should include:
- Design and development, which should include design for excellence (DfX) considerations
- New Product Introduction, or NPI, that accounts for unique requirements and customization
- Bespoke test development that can effectively detect and prevent product defaults
- Global supply chain management that extends to inventory management and reverse logistics for comprehensive product lifecycle management
- Digitally transformed manufacturing process, which should include automated workflows and data-driven autonomous manufacturing
- Fulfilment and third-party logistics, preferably in your region of distribution, to ensure supply continuity and predictability
The outsourcing manufacturing partner you choose can make or break your production process and impact your OEM business’s ability to supply products to a demanding market. When considering a contract manufacturer or EMS partner, OEMs should consider those with a vertically integrated manufacturing process that includes as many of the above services as possible, to ensure as many steps in the value chain are simplified and optimized.
Summary
Leveraging the expertise of a vertically integrated contract manufacturing partner provides substantial benefits to OEMs. Vertical integration enables greater supply chain control, improved cost management, enhanced product lifecycle efficiency, better quality control and happier end customers.
For OEM companies looking to overcome supply chain complexity and scale their operations to meet fluctuating market demands, vertically integrated manufacturing is a worthwhile strategy that optimizes production, maintains high-quality standards, and supports business agility in a dynamic market environment.
Learn more about vertical integration and the benefits it can provide for your business, or browse SVI’s vertical capabilities.
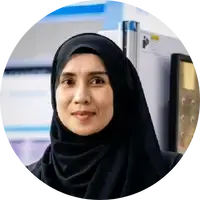