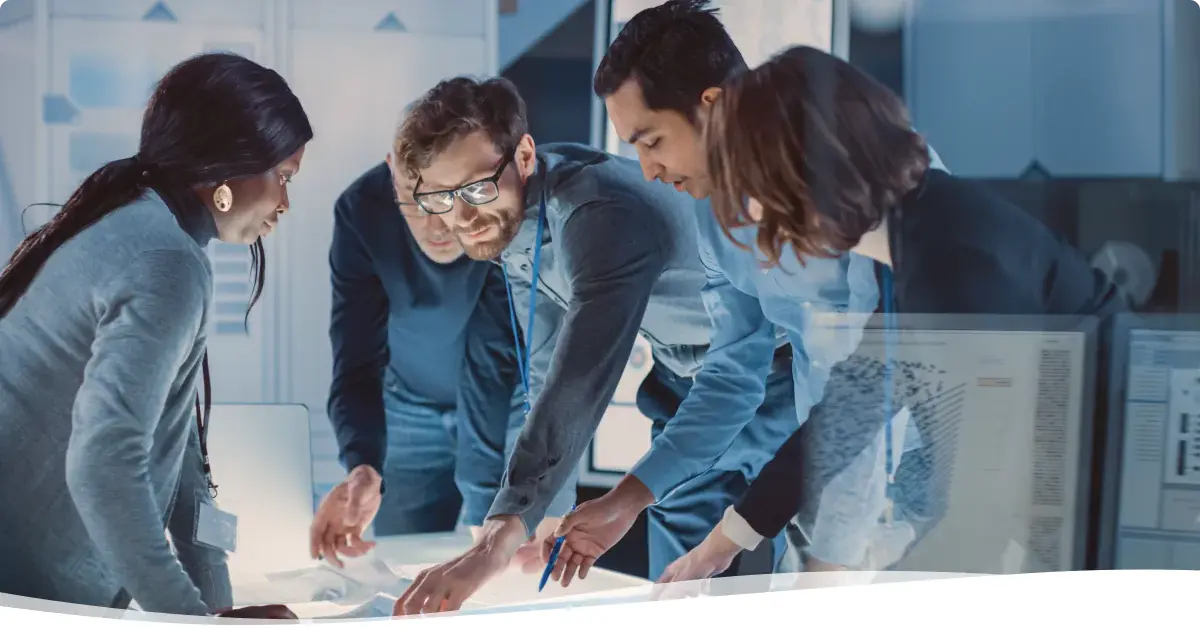
Enhancing SIOP Process Efficiency With Vertical Integration
Maintaining an optimal sales, inventory, and operations planning process that simultaneously enables cost and resource efficiency, operational flexibility, and overall business growth can be challenging. Managing risks and maintaining competitive advantage can strain the complex SIOP process for teams struggling with fluctuating market demands, global supply chain uncertainty, resource constraints, and regulatory obligations.
Incorporating a vertically integrated solution can ease the burden by providing more control and synchronization across all components of the SIOP process, ultimately leading to improved efficiency, cost savings, and customer satisfaction. For OEMs operating in complex and high-demand sectors, transitioning to a more integrated approach can enhance operational resilience.
A brief introduction to vertical integration
Vertical integration refers to how much of the production and supply chain process a contract or EMS manufacturer controls. By integrating multiple stages, manufacturers can offer OEM customers a comprehensive service suite that streamlines production, reduces costs, and enhances quality control. This model is particularly advantageous for OEMs operating in high-tech industries like automotive, aerospace, and MedTech, where precision, reliability, and speed are critical.
For OEMs, partnering with a vertically integrated manufacturing partner means gaining access to a controlled, efficient supply chain managed under one roof. This integration minimizes the complexity and risk associated with coordinating multiple suppliers, improves process alignment, speeds up decision-making, and enhances flexibility in operations.
How vertical integration enhances SIOP process components
Sales forecasting
Vertical integration significantly improves sales forecasting accuracy by consolidating control over the supply chain. When a manufacturer manages both the production and distribution stages, it gains direct access to critical data across the supply chain. This end-to-end visibility enables more precise analyses of demand patterns and consumption rates, facilitating anticipatory adjustments in production schedules and inventory management.
Additionally, by reducing dependencies on external suppliers and the associated risks of miscommunication or delays, vertical integration ensures that the forecasting data is accurate, reliably up-to-date, and easily accessible. This capability is crucial for OEMs in sectors where forecasting precision directly impacts production efficiency and market responsiveness.
Inventory management
In a vertically integrated setting, manufacturers can achieve superior inventory management, which is pivotal for maintaining cost efficiency and swiftly meeting customer demand. By overseeing the entire supply chain, manufacturing partners can more effectively synchronize the flow of materials and finished products, minimizing OEMs' stock risks.
This control extends to adjusting inventory levels dynamically based on real-time sales and supply chain data, significantly reducing lead times and enhancing service levels to OEM customers. Moreover, vertical integration allows for the implementation of Just-In-Time (JIT) manufacturing practices more effectively, as the proximity and control over supply ensure that materials are available exactly when needed, without the burden of holding large inventories.
Production planning
Vertical integration facilitates a more streamlined production planning process, essential for high-tech OEMs. With integrated operations, manufacturers can oversee all aspects of the production cycle, enhancing production planning efficiency and allowing for greater flexibility to adapt to changes in customer demand or supply chain disruptions.
The immediate access to manufacturing metrics and operational data across different production stages enables quick decision-making and adjustments in production plans and more strategic resource allocation across materials, labor, and capital. This ensures that resources are optimally allocated to meet current and projected needs without delays, as well as long-term strategic objectives.
Operations
Integrating operations under a single management umbrella allows manufacturers to optimize resource allocation and utilization, leading to substantial gains in operational efficiency for OEMs. This integration ensures that every part of the production process is aligned with the OEM's overall strategic goals, facilitating better coordination between the procurement, manufacturing, and quality control phases of production.
Signs your SIOP process needs a vertically integrated solution
Some commonly experienced challenges can indicate that your sales inventory and operations planning process could benefit from vertically integrated support. Here are some of the ways you can identify the need for vertical integration in your SIOP process:
- You face frequent stockouts or excess inventory: If you frequently experience stockouts or, conversely, hold excessive inventory levels, it could be a sign that your SIOP process lacks proper coordination and control. These inventory issues often result from poor forecasting accuracy and misaligned production scheduling, problems that vertical integration can address by improving data flow across the production chain.
- You don’t respond to market changes quickly enough: In dynamic industries, responding quickly to market shifts is crucial. If your business struggles to adjust production schedules or inventory levels swiftly in response to changing market demands, this may indicate a lack of alignment among the various stages of the supply chain. A vertically integrated structure can enhance flexibility, allowing you to react promptly and effectively.
- Operational costs remain high: If your company notices that its production costs are consistently high compared to industry benchmarks, this might be due to inefficiencies in managing multiple suppliers and logistical complexities. A vertically integrated manufacturing partner can reduce these costs by streamlining operations and reducing the need for multiple intermediaries.
- You struggle with quality control: Consistent problems with product quality can be a sign that your existing SIOP process is failing to adequately oversee and integrate quality control measures throughout the production cycle. Vertical integration provides tighter control over the complete manufacturing process, ensuring higher and more consistent quality standards.
- Communication breakdowns occur regularly: Poor communication between different supply chain stages often leads to errors and inefficiencies. Your SIOP process can suffer if information about production needs, inventory levels, and customer demands does not flow seamlessly between stages. With vertical integration, you can achieve unified communication across all stages, leading to better operational alignment.
- You're unable to scale operations effectively: Difficulty scaling operations to meet growing market demand without encountering significant disruptions or cost increases can indicate that your existing non-integrated supply chain is a limiting factor. A vertically integrated model can offer the scalability you need by ensuring that all aspects of manufacturing and supply are aligned and capable of expanding in a synchronized manner.
Conclusion
For OEMs grappling with insufficient SIOP processes resulting in high costs, limited flexibility and compromised product quality, vertical integration represents a strategic approach to manufacturing outsourcing that aligns with the growing demand for operational excellence and innovation in global high-tech markets.
A vertically integrated SIOP process translates into reliable production schedules, consistent product quality, and the ability to scale operations quickly in response to market opportunities or challenges, which are critical for maintaining competitiveness.
By partnering with a vertically integrated manufacturing partner, OEMs can achieve more accurate sales forecasting, better inventory management, strategic production planning and enhanced operations. This will, in turn, reduce supply chain woes, costs and complex supplier coordination, leaving space for enhanced flexibility, scalability and growth.
Learn more about the benefits of vertical integration in manufacturing or browse SVI’s vertically integrated services.
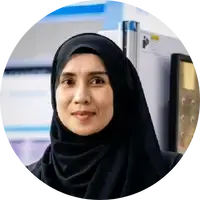