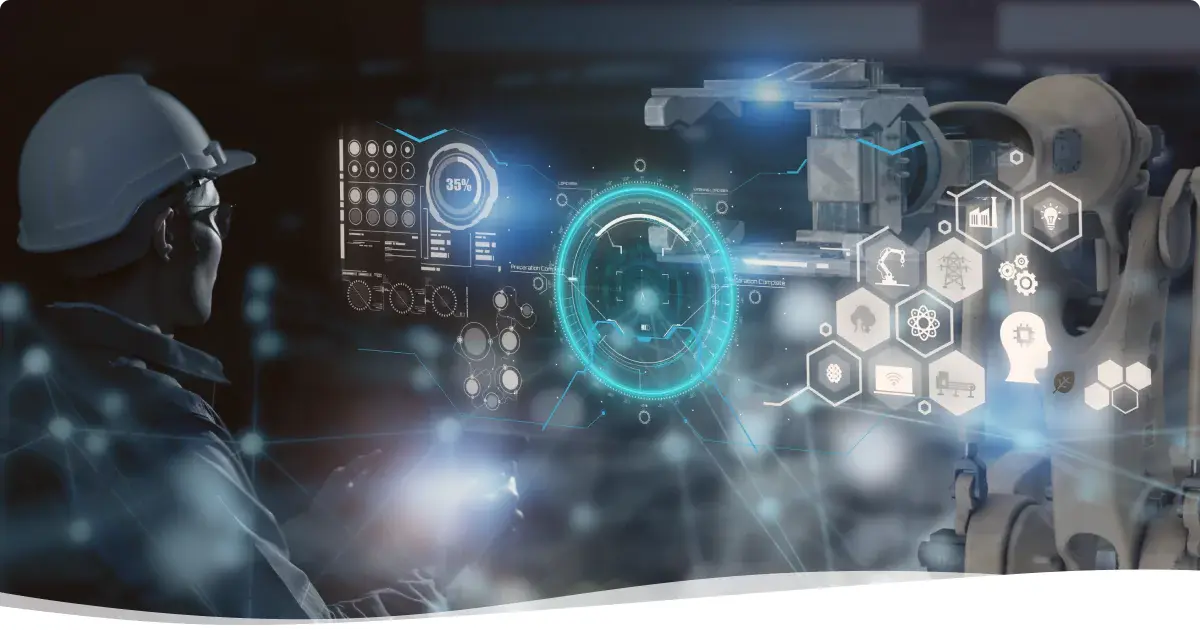
Exploring the Impact of Digital Transformation in Manufacturing
The digital transformation revolution is being felt worldwide in all industries and walks of life, and the rapidly evolving manufacturing landscape is no exception. Beyond mere automation, digital transformation in manufacturing sees sophisticated digital technologies like IoT, AI and robotics embedded into manufacturing operations, fundamentally altering how products are designed, produced, and delivered.
For OEMs, factors like operational advancement and market responsiveness are crucial, and integrating digital technologies into their manufacturing processes is no longer optional but essential for maintaining competitive advantage. By influencing production outcomes, streamlining operations and offering unprecedented agility and precision, digital transformation in manufacturing has the transformative potential to meet, and even exceed, the changing needs of today's high-tech manufacturing environment.
Core components of digital transformation in manufacturing
Below are the key technologies integral to advancing digital transformation in manufacturing, helping contract manufacturers and OEMs drive efficiency, reduce costs, and improve product quality through smart, connected, and automated solutions.
1. AI
AI in manufacturing is primarily used to optimize processes, enhance quality control, and drive innovation. It leverages machine learning algorithms to analyze vast datasets and identify patterns and insights humans might miss. For example, AI can automate the visual inspection of products using advanced image recognition, ensuring quality while significantly reducing time, human error and operational costs. The AI applications used for these tasks include predictive maintenance, quality inspection systems, and supply chain management optimizations.
2. IoT
IoT technology integrates into manufacturing by connecting various equipment and tools to a centralized network, allowing for real-time data collection and analysis. This connectivity enables manufacturers to monitor machine performance, track production metrics, and predict maintenance needs without manual intervention. For instance, IoT sensors can detect anomalies in machine behavior that may indicate a potential failure, allowing for preemptive maintenance that minimizes downtime and maximizes productivity.
3. Robotics
With integration rates expected to grow by 14% annually by 2025, robotics technology has revolutionized manufacturing floors by performing tasks that are too dangerous, tedious, or complex for human workers. Robots in manufacturing are used for assembly, welding, painting, and packing, among other tasks, improving speed and precision. These robots are often integrated with other systems via IoT to enhance their capabilities and provide real-time feedback to operators. This, in turn, increases productivity and maintains consistent product quality, especially in high-volume or precision-reliant tasks.
4. Digital twins
Digital twins are virtual replicas of physical devices manufacturers use for product simulation, analysis, and testing. These digital models allow manufacturers to predict the outcomes of changes in the manufacturing process without interrupting current production lines—crucial for future scenario planning and process refinement. By using digital twins, manufacturers can optimize their manufacturing processes, reducing costs and time to market for OEMs while improving product quality and product development cycles.
Impact on production processes
Digital transformation in manufacturing has profoundly impacted production processes by optimizing operations, enhancing product quality, and minimizing downtime. Integrating advanced digital tools allows manufacturers to achieve greater precision and efficiency, adapting to real-time changes and challenges within the production environment. For example, real-time data analytics can pinpoint inefficiencies in the production line or predict when a machine is likely to fail, enabling proactive maintenance that prevents costly unplanned downtime.
A notable example is General Electric, which has effectively implemented digital twins across its manufacturing processes to create virtual models of its machines. This enables the company to simulate production scenarios and optimize machine settings without halting actual production. This approach has significantly reduced testing time and cost, improved product quality, and quickened time-to-market for new innovations. GE's use of digital twins exemplifies how integrating digital tools can transform traditional manufacturing practices into more agile and cost-effective operations.
Vertical integration and digital transformation
The vertically integrated manufacturing strategy gives manufacturers greater control across the full production process, from sourcing raw materials to supply chain management and distribution. This leads to reduced costs, increased quality control and improved supply chain reliability for their OEM customers.
When it comes to digital transformation, vertical integration enhances a manufacturer's ability to implement comprehensive digital transformation strategies across its operations. By controlling more supply chain segments, the manufacturing partner can more effectively deploy IoT devices, AI, and data analytics tools to gather insights and optimize each production stage. A vertically integrated manufacturer might use IoT sensors across operations to monitor everything from inventory levels to machine performance. This enables real-time adjustments across the value chain that improve efficiency and reduce waste.
Operational outcomes for OEMs
Digital transformation in manufacturing has significantly transformed operational outcomes for OEMs. It facilitates increased scalability and efficiency, allowing OEMs to respond quickly to market demands or supply chain fluctuations before they cripple operations. Digital tools enable manufacturers to simulate different production scenarios and outcomes, optimizing operations without risking actual production. This capability is crucial for OEMs operating in volatile markets or struggling to coordinate multiple supplier relationships simultaneously.
Furthermore, digital transformation inherently leads to reduced operational costs. Automated systems and robotics decrease the need for labor-intensive processes, minimizing human error and enhancing productivity, while advanced analytics significantly cut unexpected repair costs and prolong equipment life.
Future digital transformation trends and innovations
Digital transformation is set to evolve in the manufacturing industry as technology advances. Here are some key trends for manufacturers and OEMs to watch in the coming years:
- Increased integration of AI and machine learning: AI integration in manufacturing will likely go beyond predictive maintenance and quality control to include more advanced functions like real-time supply chain optimization and dynamic pricing models. AI will also enhance customization capabilities, allowing manufacturers to offer OEMs highly personalized product manufacturing at scale.
- Autonomous robotics and Cobots: Autonomous and collaborative robots (cobots) will likely become more popular as these technologies become more dexterous, intelligent and safe. Cobots are designed to work alongside humans, enhancing their capabilities rather than replacing them. They will help with labor shortages in certain markets and improve workplace safety by taking on dangerous tasks.
- Blockchain for supply chain transparency and security: By providing a secure, immutable ledger, blockchain can enable greater transparency and traceability of materials and components, revolutionizing manufacturing supply chain management. This will be especially vital for industries where material certification and compliance (like aerospace and pharmaceuticals) is critical and could help combat counterfeit products.
- Sustainability driven by digital tools: As global emphasis on sustainability grows, manufacturers will increasingly leverage digital transformation to not only cut costs but also reduce their environmental impact. This includes everything from energy-efficient production processes enabled by AI and IoT to enhanced waste management through digital tracking systems.
How SVI leverages digital transformation in manufacturing
Cost reduction, improved product quality, and speed to market are all key factors for OEMs aiming to maintain their competitive edge in their respective high-tech industries. With these objectives in mind, SVI employs digital transformation tactics to enhance decision-making, operational agility and operational excellence, ensuring OEMs can consistently reap the benefits of digital transformation for sustained growth and market leadership.
SVI ensures exceptional production control and adaptability by integrating digital tools such as automated robotics and advanced data analytics into our vertically integrated production process. This accelerates the innovation cycle while driving down costs, allowing us to meet OEMs' high standards and dynamic needs across industries. This strategy showcases how vertical integration and digital transformation provide a robust framework for manufacturing excellence and competitive advantage in the global market.
Conclusion
Digital transformation in manufacturing offers manufacturers a golden opportunity to provide unparalleled manufacturing service to their OEM customers. By leveraging technologies like AI, IoT, robotics and digital twins, EMS and contract manufacturing partners can streamline the entire value chain, helping OEMs achieve their growth objectives while addressing key challenges like supply chain uncertainty and cost pressures.
As technological advances become increasingly prevalent, integrating cutting-edge solutions will make staying competitive in an ever-evolving industry much more attainable for OEMs, especially if they partner with the right, digitally transformed manufacturing partners.
Embrace digital transformation in manufacturing with SVI
SVI's focus on continuous improvement and embracing revolutionary technologies ensures that we keep pace with industry standards and often set them. By investing in ongoing innovations like digital factory implementations and refining our vertical business model, we are well-positioned to meet the evolving demands of OEMs, aligning with their market needs and future growth trajectories for long-term, mutually beneficial success.
Explore our digitally enabled services or contact us to learn how we can support your digital transformation strategies.
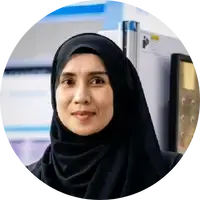