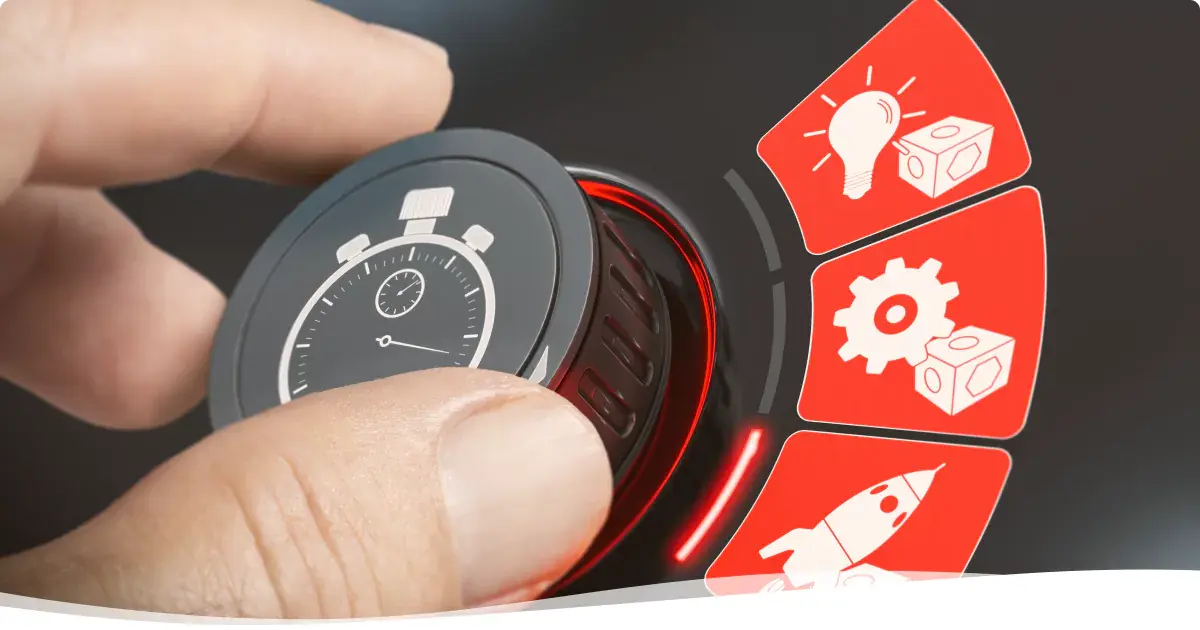
Accelerating OEM Market Launch Through An Effective NPI Process
In a global manufacturing and supply chain environment that is both fast-evolving and unpredictable, quickly launching a product to market is crucial for competitiveness but also challenging to achieve. This is where an effective New Product Introduction (NPI) process proves essential for achieving a quick time-to-market and ensuring products are not only launched faster but of a consistently high quality and reliability standard.
But the importance of a well-structured NPI process extends beyond speed; it also fosters innovation and ensures scalability. For OEMs operating in high-tech industries, a solid NPI process is a critical component for driving growth and sustaining market leadership. By streamlining the various stages of product development—from initial concept to full-scale production—an efficient NPI process helps mitigate risks, reduce costs, enhance overall project management, and ultimately accelerate OEMs' journey from initial idea to market-ready product.
What does an effective NPI process look like?
An effective New Product Introduction process is a structured and systematic approach to taking a new product from initial concept to full-scale production and market release. When optimized, an effective NPI process ensures that new products meet quality and compliance standards, are manufacturable, and align with market demands.
Critical components of an effective NPI process include thorough planning, leveraging digital transformation, and robust project management. It involves a series of well-defined steps, including:
- Concept development: Ideas are generated and evaluated for feasibility
- Design: Detailed specifications are created, and prototypes are developed
- Prototyping: The initial physical creation of the product
- Testing: Rigorous testing of the initial prototype to identify issues.
- Validation: The product is validated against the necessary specifications, ensuring it meets all standards and requirements.
- Production ramp-up: Scaling up manufacturing processes to prepare for market launch.
Each step in the NPI process requires close collaboration between various teams, such as DFX, manufacturing, and supply chain, to ensure that all aspects of the product and its manufacturing process are optimized for market release on time and within budget.
The significance of NPI for accelerating time-to-market
Time-to-market is key to maintaining competitive advantage, particularly in fast-paced industries. By systematically managing the development and launch phases, an effective NPI process helps OEMs streamline operations, reduce bottlenecks, and mitigate risks that can delay market entry. This process ensures that all aspects of product development, from design to production, are carefully planned and executed, resulting in faster product launches.
Industries such as Automotive, MedTech, and Industrial Automation, in particular, benefit from reduced TTM due to their rapidly evolving technological landscapes and intense competition. For instance, the ability to swiftly bring innovative features to market in the Automotive sector can significantly influence market share. In MedTech, accelerated TTM can improve patient outcomes by providing timely access to advanced medical devices. Similarly, faster product introductions in Industrial Automation can help companies quickly seize innovation opportunities. Overall, a well-executed NPI process speeds up product launches, putting businesses ahead in the market.
Other benefits of an optimized NPI process for OEMs
Apart from a sped-up TTM, an effective NPI process also brings additional benefits to OEMs, which can all contribute to helping businesses keep pace with their respective markets and customer expectations.
1. Cost efficiency
With an effective NPI process, OEMs can drive cost efficiencies by minimizing resource wastage and errors throughout the production process. By integrating detailed planning and iterative testing at each stage, companies can identify and rectify potential issues early, reducing the need for costly reworks and ensuring resources are used optimally. This proactive approach not only conserves materials and labor but also shortens development timelines, allowing for a more efficient allocation of budgets and improved profitability.
2. Improved product quality
The rigorous testing and validation stages inherent in a robust NPI process are crucial for guaranteeing a high-quality final product. Each prototype undergoes extensive evaluation to verify that it meets predefined standards and performs reliably under various conditions. This meticulous attention to detail helps prevent defects and enhances the product's overall reliability, leading to greater customer satisfaction and loyalty. Consistently high-quality products bolster an OEM's reputation, fostering trust and customer retention while mitigating the risks associated with recalls due to product failures and faults.
3. Scalability and flexibility
An effective NPI process also equips OEMs with the scalability and flexibility needed to respond swiftly to changes in market demand. The process includes strategic planning for production scalability, allowing companies to adjust production volumes and introduce new variants quickly. This adaptability is essential for staying competitive in dynamic markets, enabling OEMs to capitalize on emerging opportunities and meet diverse customer needs efficiently. Such flexibility ensures businesses can grow and evolve in response to market trends while maintaining the operational efficiency that underpins a rapid time-to-market.
Key strategies for implementing an effective NPI process
Implementing an effective NPI process requires a strategic approach that leverages the capabilities and expertise of a high-tech, vertically integrated production partner. Here are three key strategies that can deliver an efficient and successful NPI process:
1. Vertical integration
Vertical integration is a strategic approach that can significantly enhance the efficiency and effectiveness of the NPI process. By consolidating multiple stages of production and development within their own purview, vertically integrated manufacturing partners give OEMs greater control over quality, timelines, and costs.
This seamless coordination across different functions—from design and prototyping to manufacturing and supply chain management—enables faster decision-making and reduces dependencies on multiple external suppliers. Partnering with a vertically integrated EMS provider also facilitates better alignment with strategic goals, ensuring that every aspect of the product development process is optimized for speed, quality, and cost-efficiency.
2. Technology and innovation
Leveraging advanced digital technologies and fostering innovation are critical strategies for implementing an effective NPI process. Tools such as computer-aided design (CAD), simulation software, and automated testing platforms enhance precision and speed up development cycles.
Additionally, incorporating digital factory concepts and factory automation streamlines production, reduces human error, and increases overall efficiency. By partnering with manufacturing suppliers at the forefront of technological advancements, companies can ensure their NPI processes are both cutting-edge and highly efficient, leading to faster and more reliable product launches.
3. Continuous improvement
Continuous improvement is a cornerstone of an effective production process overall, including the NPI process. It ensures that every iteration builds on the previous one's successes and lessons learned. Implementing methodologies like LEAN and Six Sigma fosters a culture of ongoing enhancement, where processes are regularly reviewed and optimized. This helps identify and eliminate inefficiencies and promotes a proactive attitude towards quality and performance. By continuously refining their NPI processes, manufacturers can help OEMs maintain high standards, adapt to new challenges swiftly, and drive long-term success.
Summary
An effective NPI process is indispensable for OEMs aiming to achieve swift time-to-market while maintaining high standards of quality and reliability. The current global manufacturing and supply chain landscape underscores the necessity of such processes, with industry uncertainties and digital advancements driving the need for innovation and efficiency. OEMs can navigate these complexities with greater agility and precision by leveraging advanced technologies, promoting continuous improvement, and partnering with a vertically integrated manufacturing partner.
As the manufacturing sector continues to evolve, the role of a robust NPI process in sustaining market success will only grow more critical. OEMs that prioritize optimizing their NPI processes will accelerate their product launches and enhance their ability to respond to market demands and competitive pressures. Ultimately, a well-executed NPI strategy positions OEMs to thrive in the dynamic and challenging global market, ensuring long-term growth and sustained leadership.
Explore the benefits of partnering with a high-tech, vertically integrated EMS partner, or contact SVI for more information on an effective NPI process.
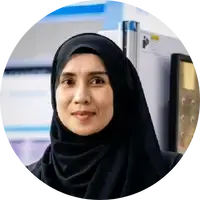