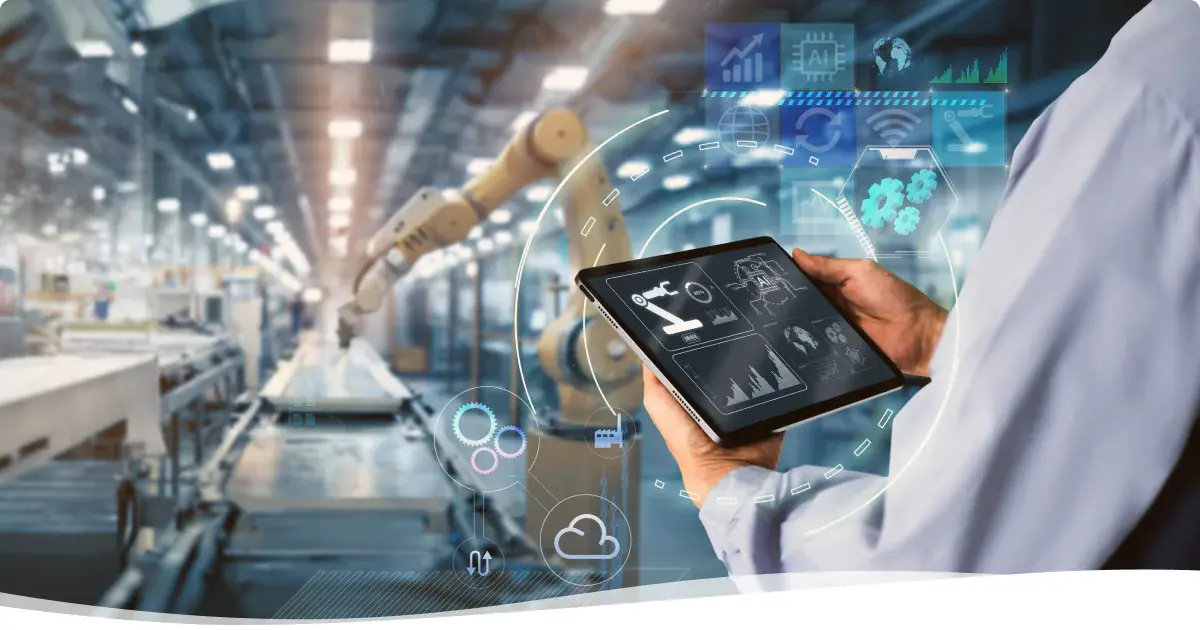
8 Benefits of Automation in Manufacturing and How to Unlock Them
The manufacturing industry is experiencing a major transformation due to swift progress in automation. Once considered a luxury, automation in manufacturing has now become essential for staying competitive in the global market. It enables manufacturers to achieve unprecedented levels of efficiency and productivity, cut costs, and improve product quality and consistency. This shift meets the growing demand for precision and customization while addressing the need for scalability and sustainability that businesses are increasingly prioritizing.
However, the journey towards fully leveraging automation's potential is intricate and requires more than just adopting new technologies. It entails a comprehensive strategy that includes vertically integrated and digitally transformed operations, which manufacturers must navigate by adopting innovative practices and forming strategic partnerships with experienced EMS providers who can guide and facilitate this transition.
8 benefits of automation in manufacturing
With the global logistics automation market boasting a predicted CAGR of 14.7%, the impact of automation in manufacturing is seen both directly in the manufacturing process itself and indirectly in the outcomes of these automated processes. Here are eight of the main benefits of automation:
- Increased efficiency and productivity: Automation in manufacturing translates directly into higher efficiency and productivity. Automated machinery works consistently without breaks, delays, or needing to shift between tasks, significantly speeding up production processes. This relentless process automation ensures that projects stay on schedule, reducing downtime and increasing output, all while maintaining a high level of performance throughout.
- Enhanced quality and consistency: Automated systems are pivotal to maintaining stringent quality standards and ensuring product consistency. By reducing human error, these systems consistently produce parts or products within precise specifications, leading to fewer defects and reworks. Automation also facilitates real-time monitoring and quality control, ensuring each product meets the required standards before it moves further down the production line.
- Cost reduction: One of the most significant advantages of automation is cost reduction. By automating repetitive and labor-intensive tasks, manufacturers can reduce the need for manual labor, which often leads to long-term savings in wage costs. Additionally, automation minimizes material waste through precise resource control during manufacturing, further cutting costs associated with excess materials and inefficient resource use.
- Improved worker safety: Automation significantly enhances worker safety by handling dangerous tasks and reducing human interaction with hazardous machinery or toxic materials. This minimizes the risk of accidents and improves overall workplace health and safety standards. Automating dangerous processes means workers are less likely to encounter potentially life-threatening situations, leading to a safer, more secure working environment.
- Scalability: A key priority for expanding businesses, automation enables manufacturers to scale their operations quickly to meet market demands or adjust to new production requirements. Whether scaling up to increase output or scaling down to reduce costs, automated systems can be adjusted without the extensive retraining or hiring phases that manual operations require, allowing manufacturers to respond swiftly to OEM needs as they navigate changing industry dynamics.
- Data collection and analysis: Automated manufacturing systems are equipped with sensors and digital tools that collect vast data from the production process. This data is invaluable for gaining insights into operational efficiencies, maintenance needs, and opportunities for process improvements. Advanced data analytics can help predict potential failures and optimize production schedules, enhancing decision-making and strategic planning.
- Sustainability: Automation contributes to sustainability in manufacturing through more efficient resource use and waste reduction. Automated systems are precise, significantly decreasing material waste and energy consumption. This precision, combined with the reduced need for rework and disposal of defective products, supports manufacturers in achieving their environmental goals and reducing their carbon footprint and that of their OEM customers.
- Enhanced competitiveness: In today's fast-paced market, quickly adapting and delivering high-quality products is crucial. Automation enhances an OEM's competitiveness by speeding up their time to market and supporting customization in response to customer demands. This agility helps manufacturers meet and exceed customer expectations, fostering loyalty and driving business growth.
Unlocking the benefits of automation
So, how do OEMs tap into automation to experience these benefits? Here are four fail-proof ways to accelerate the adoption and advancement of automation in manufacturing and fully harness its advantages.
1. Vertical integration
Vertical integration is a strategic approach that can greatly amplify the benefits of automation in manufacturing. Manufacturers that leverage vertical integration can achieve a seamless flow of operations by controlling multiple stages of the production process under one roof, from raw materials to final assembly and distribution, supporting industrial automation efforts and enhancing its effectiveness across the value chain. For OEM customers, this means minimized delays, reduced operational complexity and faster turnaround times, making implementing changes and maintaining quality control throughout production easier.
2. Digital transformation
Digital transformation in manufacturing revolves around integrating advanced automation technologies like AI and IoT into various aspects of the production process. These technologies enhance the effectiveness of factory automation by enabling machines to make intelligent decisions, predict maintenance needs, and adapt to changing conditions automatically without human intervention. This level of smart automation streamlines operations and significantly boosts productivity and operational efficiency.
3. Strategic planning and continuous improvement
Strategic planning in the context of automation involves a forward-looking approach that anticipates future needs and challenges to ensure the implementation of automation is both strategic and beneficial over the long term. Continuous improvement methodologies, such as LEAN and Six Sigma, play a significant role in minimizing waste and optimizing processes. By integrating these methodologies with automation, manufacturers can continually refine their operations, ensuring they remain agile and responsive to market and technology changes.
4. Partnering with technologically advanced EMS partners
Choosing the right EMS and contract manufacturing partner is crucial for OEMs aiming to capitalize on the benefits of automation. The ideal partner should possess the technological capabilities and a proven track record in successfully implementing automation across various manufacturing processes. This partnership allows manufacturers to leverage expertise in automation that may be too complex or costly to develop in-house, ensuring they stay ahead of technological advancements and swiftly adapt to new manufacturing trends and standards.
An EMS provider with robust digital transformation and automation capabilities can help streamline production processes, reduce time to market, and improve product quality, thereby enhancing overall business competitiveness for OEMs.
Conclusion
The transformative impact of automation in manufacturing is evident across several dimensions—from boosting efficiency and productivity to enhancing quality and competitive advantage. As the manufacturing landscape evolves, automation integration becomes essential for manufacturers looking to stay ahead in a competitive market. By embracing automation, OEMs can significantly reduce costs, improve safety standards, and achieve greater operational scalability and sustainability.
To fully unlock these benefits, manufacturers must consider strategic partnerships with experienced EMS providers like SVI. With expertise in vertical integration, digital transformation, and strategic planning, manufacturing partners like us are uniquely positioned to help OEMs optimize their automation investments. Our approach ensures that automation is implemented and continuously improved while aligning with your needs and goals.
Explore our services to learn more about how we use automation in our manufacturing processes or contact us to find out how we can support your automation strategy.
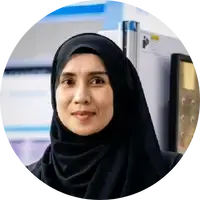